Destylator przemysłowy to zaawansowane urządzenie, które odgrywa kluczową rolę w procesach separacji i oczyszczania substancji chemicznych. W jego budowie wyróżniamy kilka istotnych komponentów, które wpływają na efektywność działania całego systemu. Jednym z najważniejszych elementów jest kolumna destylacyjna, która jest odpowiedzialna za separację składników na podstawie różnicy ich temperatur wrzenia. Wewnątrz kolumny znajdują się różne elementy, takie jak tace czy złoża, które zwiększają powierzchnię kontaktu między parą a cieczą, co sprzyja efektywnemu procesowi destylacji. Kolejnym kluczowym elementem jest kondensator, który schładza parę i przekształca ją z powrotem w ciecz. Oprócz tego, istotne są również zbiorniki do gromadzenia zarówno surowców, jak i produktów końcowych. Warto również zwrócić uwagę na systemy kontroli temperatury i ciśnienia, które zapewniają optymalne warunki pracy destylatora.
Jakie zastosowania ma destylator przemysłowy w przemyśle
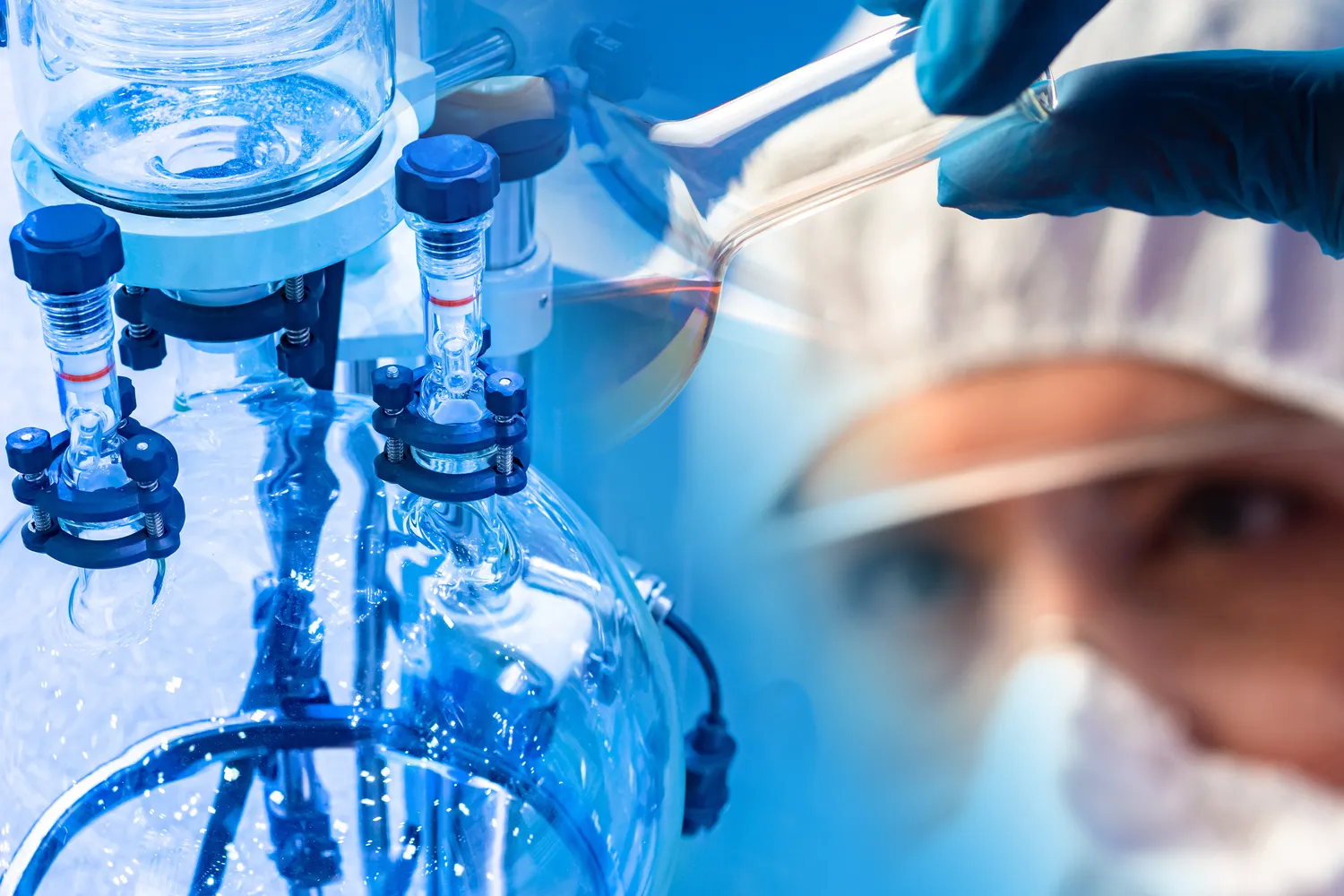
Destylator przemysłowy znajduje szerokie zastosowanie w różnych branżach, co czyni go niezwykle wszechstronnym narzędziem. Przede wszystkim jest wykorzystywany w przemyśle chemicznym do oczyszczania i separacji substancji chemicznych. Dzięki procesowi destylacji możliwe jest uzyskanie wysokiej czystości produktów, co jest kluczowe w produkcji farmaceutyków oraz kosmetyków. W przemyśle petrochemicznym destylatory służą do rozdzielania frakcji ropy naftowej, co pozwala na uzyskanie paliw oraz innych produktów chemicznych. Kolejnym obszarem zastosowań są zakłady produkujące napoje alkoholowe, gdzie destylacja jest niezbędna do uzyskania odpowiedniej jakości trunków. W przemyśle spożywczym destylatory mogą być wykorzystywane do ekstrakcji aromatów oraz olejków eterycznych z roślin. Również w sektorze biotechnologicznym destylacja odgrywa ważną rolę w procesach fermentacji i odzyskiwania produktów ubocznych.
Jakie są zalety stosowania destylatora przemysłowego
Stosowanie destylatora przemysłowego niesie ze sobą wiele korzyści, które przyczyniają się do zwiększenia efektywności procesów produkcyjnych. Po pierwsze, dzięki możliwości separacji składników na podstawie ich temperatur wrzenia, destylacja pozwala na uzyskanie wysokiej czystości produktów końcowych. To z kolei przekłada się na lepszą jakość finalnych wyrobów, co jest szczególnie istotne w branżach takich jak farmaceutyka czy kosmetyki. Ponadto, nowoczesne destylatory charakteryzują się dużą wydajnością oraz możliwością pracy w trybie ciągłym, co znacząco podnosi efektywność produkcji. Kolejną zaletą jest możliwość automatyzacji procesu destylacji, co pozwala na redukcję kosztów operacyjnych oraz minimalizację ryzyka błędów ludzkich. Destylatory przemysłowe są także elastyczne i mogą być dostosowane do różnych rodzajów surowców oraz produktów końcowych. Dzięki temu można je stosować w różnych gałęziach przemysłu bez konieczności inwestowania w nowe technologie.
Jakie są najnowsze technologie w dziedzinie destylatorów przemysłowych
W ostatnich latach rozwój technologii związanych z destylatorami przemysłowymi przeszedł znaczną ewolucję, co wpłynęło na ich wydajność oraz funkcjonalność. Jednym z najważniejszych trendów jest automatyzacja procesów produkcyjnych, która pozwala na zdalne monitorowanie i kontrolowanie parametrów pracy urządzeń. Dzięki zastosowaniu nowoczesnych systemów informatycznych możliwe jest optymalizowanie procesów destylacji w czasie rzeczywistym, co prowadzi do zwiększenia efektywności energetycznej oraz redukcji kosztów operacyjnych. Kolejną innowacją są zaawansowane materiały konstrukcyjne stosowane w budowie kolumn i kondensatorów, które charakteryzują się lepszymi właściwościami termicznymi oraz odpornością na korozję. Warto również wspomnieć o technologii membranowej, która staje się coraz bardziej popularna jako alternatywa dla tradycyjnej destylacji w niektórych aplikacjach. Dzięki niej możliwe jest uzyskanie jeszcze wyższej czystości produktów przy niższych kosztach energetycznych. Również rozwój technologii odzysku ciepła pozwala na zwiększenie efektywności energetycznej całych instalacji przemysłowych.
Jakie są koszty związane z zakupem destylatora przemysłowego
Koszty zakupu destylatora przemysłowego mogą się znacznie różnić w zależności od wielu czynników, takich jak typ urządzenia, jego wydajność oraz dodatkowe funkcje. Na rynku dostępne są zarówno proste modele, które można nabyć za stosunkowo niewielką kwotę, jak i zaawansowane systemy, które wymagają znacznych inwestycji. W przypadku prostych destylatorów laboratoryjnych ceny mogą zaczynać się od kilku tysięcy złotych, natomiast bardziej skomplikowane urządzenia przemysłowe mogą kosztować nawet kilkaset tysięcy złotych. Warto również uwzględnić dodatkowe koszty związane z instalacją oraz uruchomieniem urządzenia, które mogą być znaczące w przypadku dużych systemów. Oprócz kosztów zakupu należy także brać pod uwagę wydatki związane z eksploatacją destylatora, takie jak zużycie energii, konserwacja oraz ewentualne naprawy. Dobrze zaplanowana inwestycja w destylator przemysłowy powinna uwzględniać wszystkie te aspekty, aby zapewnić optymalizację kosztów w dłuższym okresie.
Jakie są najczęstsze problemy z destylatorami przemysłowymi
Destylatory przemysłowe, mimo swojej zaawansowanej technologii, mogą napotykać różne problemy podczas eksploatacji. Jednym z najczęstszych kłopotów jest zatykanie kolumny destylacyjnej, co może prowadzić do obniżenia efektywności procesu separacji. Zatykanie to często spowodowane jest osadami chemicznymi lub zanieczyszczeniami obecnymi w surowcach. Innym problemem może być niewłaściwe ustawienie parametrów pracy, takich jak temperatura czy ciśnienie, co może skutkować nieefektywną destylacją i obniżoną jakością produktów końcowych. Kolejnym wyzwaniem są awarie kondensatorów, które mogą prowadzić do strat materiałowych oraz zwiększenia kosztów produkcji. W przypadku starszych modeli destylatorów mogą występować również problemy związane z korozją materiałów konstrukcyjnych, co wymaga regularnej konserwacji i wymiany części. Aby minimalizować ryzyko wystąpienia tych problemów, kluczowe jest przeprowadzanie regularnych przeglądów technicznych oraz stosowanie odpowiednich procedur operacyjnych.
Jakie są różnice między destylatorami przemysłowymi a laboratoryjnymi
Destylatory przemysłowe i laboratoryjne różnią się przede wszystkim skalą produkcji oraz przeznaczeniem. Destylatory laboratoryjne są zazwyczaj mniejsze i służą do przeprowadzania eksperymentów oraz badań naukowych na niewielką skalę. Ich konstrukcja jest dostosowana do potrzeb laboratorium i często charakteryzują się większą elastycznością w zakresie zmiany parametrów pracy. Z kolei destylatory przemysłowe są zaprojektowane do pracy w trybie ciągłym i mają znacznie większą wydajność, co pozwala na przetwarzanie dużych ilości surowców w krótkim czasie. Ponadto, destylatory przemysłowe często wyposażone są w zaawansowane systemy automatyzacji oraz monitorowania procesów, co zwiększa ich efektywność i bezpieczeństwo pracy. Różnice te wpływają również na koszty zakupu i eksploatacji obu typów urządzeń; destylatory przemysłowe wymagają większych inwestycji początkowych oraz wyższych kosztów utrzymania ze względu na ich skomplikowaną budowę i większe wymagania dotyczące konserwacji.
Jakie są najlepsze praktyki przy użytkowaniu destylatora przemysłowego
Aby zapewnić prawidłowe działanie destylatora przemysłowego oraz maksymalizować jego wydajność, warto przestrzegać kilku najlepszych praktyk związanych z jego użytkowaniem. Przede wszystkim kluczowe jest regularne przeprowadzanie konserwacji oraz przeglądów technicznych urządzenia. Dzięki temu można szybko wykrywać ewentualne usterki i zapobiegać poważniejszym awariom. Ważne jest również monitorowanie parametrów pracy destylatora, takich jak temperatura czy ciśnienie, aby upewnić się, że proces przebiega zgodnie z założeniami technologicznymi. Kolejnym istotnym aspektem jest odpowiednie szkolenie personelu obsługującego urządzenie; dobrze przeszkoleni pracownicy będą w stanie szybko reagować na wszelkie nieprawidłowości oraz podejmować właściwe decyzje w trakcie pracy. Należy także dbać o jakość surowców wykorzystywanych w procesie destylacji; ich czystość ma bezpośredni wpływ na jakość produktów końcowych oraz efektywność całego procesu.
Jakie są przyszłe kierunki rozwoju technologii destylacji przemysłowej
Przemysłowa technologia destylacji stale się rozwija i ewoluuje w odpowiedzi na rosnące potrzeby rynku oraz wyzwania związane z ochroną środowiska. Jednym z głównych kierunków rozwoju jest zwiększenie efektywności energetycznej procesów destylacyjnych poprzez zastosowanie innowacyjnych technologii odzysku ciepła oraz wykorzystania energii odnawialnej. Wprowadzenie bardziej zaawansowanych systemów automatyzacji pozwala na lepsze zarządzanie procesami produkcyjnymi oraz minimalizację strat materiałowych. Kolejnym istotnym trendem jest rozwój technologii membranowej jako alternatywy dla tradycyjnej destylacji; ta metoda może okazać się bardziej efektywna w niektórych zastosowaniach i przyczynić się do redukcji kosztów operacyjnych. Również rosnące zainteresowanie biotechnologią prowadzi do poszukiwania nowych metod ekstrakcji składników aktywnych z surowców naturalnych przy użyciu nowoczesnych technologii destylacyjnych. W miarę jak branża staje się coraz bardziej świadoma kwestii ekologicznych, można spodziewać się dalszego rozwoju technologii mających na celu ograniczenie emisji gazów cieplarnianych oraz zmniejszenie zużycia zasobów naturalnych podczas procesów produkcyjnych.